Original article is provided by our partners and spray foam providers - ThermoFoam, it can be found following this link.
Introduction:
If you are reading this article, you may be looking for answers to the following questions:
Should I get spray foam in my home?
Does spray foam insulation cause rot?
Can I sell my home with spray foam?
Can I get a mortgage with spray foam?
What can I do if I have spray foam?
Can spray foam be removed?
We’ve created this article to help provide an honest appraisal of the situation related to spray foam insulation in existing homes and the problem of homeowners whose prospective buyers can’t always get mortgages as a result. We hope that you find this article provides some clarity about spray foam insulation and why some mortgage lenders paused lending for a short period until certain industry standards were identified and implemented. Despite a rise in opportunistic companies offering spray foam removal services, removal should always be the very last option for a homeowner.
Overview
It’s no secret that the Spray Foam Industry has been in the spotlight recently regarding some homes being rejected for a mortgage. The discussions about the suitability of Spray Foam Insulation when used in a home’s pitched roof area started in November 2021 when the PCA and RPSA issued a joint report highlighting their concerns over the product and its use.
The document highlighted concerns about the correct installation of open and closed cell foams, the science behind the product, the quality of the installers, the sales process and the documentary evidence handed over to the customer once an installation had taken place. Whilst the documentation released was somewhat damning about the spray foam industry, it also served as a chance for it to come together with the PCA, RPSA, various mortgage lenders, building surveyors and other notable industry experts to discuss concerns and implement practices that could provide reassurance.
In late 2022, a Working Group was established to create the parameters for a new inspection protocol that should guide surveyors and lenders when they encounter homes with spray foam insulation. The documents’ purpose was to offer guidance to building surveyors so that they could conclude whether the insulation posed a low, medium or high risk to the property.
Much of the dislike or concerns with spray foam are because it is spray-applied to the underside of the roof membrane, therefore covering the roof from the underside and limiting a surveyor’s ability to assess the condition of the roof. Whilst this is a justified concern, it is worth noting that there are many instances where a surveyor would be unable to see the underside of the roof to assess its condition, for example, in Dormer Bungalows. Of course, in many cases, surveyors were unable to review documentation that supported the purpose and considered the risks of having spray foam insulation installed. Additionally, most existing homes have a high-resistance, non-breathable bitumen felt-style membrane which can present internal moisture from escaping from the home. When these concerns are considered, it is easy to understand why there is much confusion over what constitutes a good or bad spray foam installation.
What Is Spray Foam Insulation?
There are two types of spray foam insulation: a high-density, partially breathable closed-cell foam and a low-density, very-breathable open-cell foam. Closed-cell foam was introduced into the UK in the 1980s and was mainly used in industrial environments. It also found its way into UK homes thanks to its ability to bond and strengthen failing roofs where roofing membranes were damaged or weren’t present. Whilst effective at prolonging the life of a roof, closed-cell foam can also cause enhanced decay of the structure if moisture becomes trapped within the roof structure. This was a point led the PCA and RPSA to highlight the risks of spray foam insulation.
Open Cell Foam is a low-density, breathable product that started to gain popularity from 2012 onwards. Sprayed directly to the underside of roofing felts, it provides an airtight yet breathable thermal seal of the roof space, which helps to conserve energy and make a home more energy efficient. In addition, Open Cell spray foam can offer excellent sound attenuation whilst freeing up space on the loft floor for storage. It can also perform with the life of the property without degrading or deteriorating, often guaranteed by the installer for a period of 25-years.
When installed as a direct-to-tile, roof stabilisation system, the roof itself maybe experiencing fatigue and may have reached the end of its natural life, therefore requiring replacement. Whilst closed-cell foam is very effective at extending the life of the roof for an indefinite period, naturally, many homeowners saw it as a cheaper alternative to replacing the replacing the roof. Interest from homeowners was not least because some spray foam companies were activity promoting roof stabilisation solutions in the national press. Whilst previously certified as an accepted practice, direct to tile, roof stabilisation is no longer endorsed, certified or accepted as a viable option and when the roof has come to the end of its natural life, the only option is for replacement.
As insulation and thermal upgrades have become such an important part of helping homeowners to control energy costs and reduce their carbon footprint, open cell foam grew in popularity throughout the 2010’s. During the 2020-2021 Government Green Homes Grant, spray foam insulation was an approved installation measure which saw a rapid growth of its use in UK homes. The Green Homes Grant saw many installers become PAS 2030 certified which led to more stringent lodgements of installations onto the Trustmark database along with the opportunity for more surveillance of installers by the certification bodies issuing the PAS 2030 accreditations.
You can also learn more about the science behind spray foam insulation by visiting our article here: https://vpfoamspray.co.uk/about#sfi
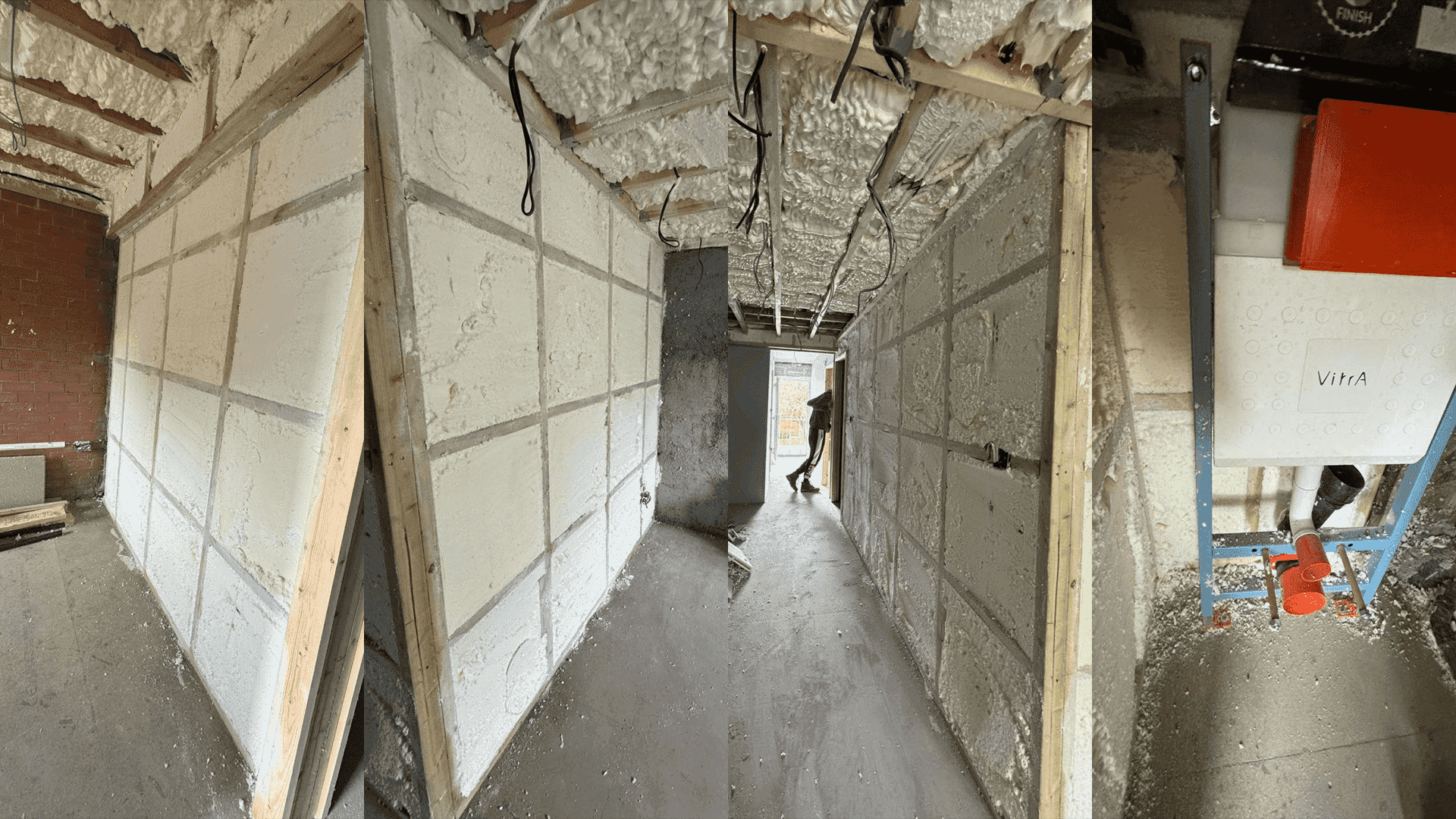
Spray Foam Mortgage Issues
Until earlier in 2023, mortgage lenders had paused offering mortgage lending on homes where spray foam insulation was installed. As a result of the Inspection Protocol documents and the efforts of the Working Group, several lenders are now prepared to accept spray foam as a viable insulation material, provided there is evidence and paperwork to show that it has been installed correctly as per approved product certification in the form of a BBA or KIWA certificate. Whilst there is a long way to go to dispel the myths of spray foam insulation completely, good progress has been made and will continue to be made but thats not to say there aren’t a vast number of non-compliant and shoddy installations that require remedy or removal.
Closed Cell Foam, when applied directly to roof tiles, is no longer an accepted insulation method due to the elevated risks attached to its application. Conversely, open cell foam, installed directly to a low-resistance roof membrane, is a very low-risk installation provided the roof is in good condition before installation and all necessary evidence has been compiled to show a compliant installation. When high resistance, bitumen felt style membranes are in situ, spray foam can still be installed, with consideration that a ventilation card should be inserted between the rafters to create airflow above the insulation or a vapour control layer is installed to the warm side of the spray foam insulation. BBA and KIWA certification recommend that a condensation risk analysis is conducted prior to the installation of spray foam insulation and most, if not all manufacturers and distributors now support their customers with this documentation. Additionally, closed cell spray foam, installed directly to high-resistance, bitumen felt-style membranes can also be classed as low-risk in southern areas of the UK.
It is essential to highlight that the RPSA and PCA Joint Position on Spray Foam Insulation, released in November 2021, was retracted in October 2022. This doesn’t mean the findings highlighted in the initial statement weren’t relevant or required further action. Still, it did help to cool the frustration between various bodies, enabling proactive discussions to take place. Under Government Guidance, the surveying, lending, and spray foam industry came together in what was an industry first and a milestone in establishing a more compliant future for this insulation material.
Fundamentally, if installed correctly in conjunction with BBA or KIWA certification, homeowners, lenders, and surveyors should feel comfortable that spray foam is a viable insulation solution for a home. In return, manufacturers/distributors, such as us, must ensure that the installers who buy our materials are adequately trained, subscribe to, and follow a set of principles that meet modern regulations. If the industry can move towards providing evidence, rationale, and science to support an installation, the spray foam mortgage issues will likely become a thing of the past.
Of course, this doesn’t help homeowners who have already had spray foam installed. With a reported 250,000 homes that have spray foam already installed, it’s likely that without the evidence that the spray foam was installed correctly following its BBA or KIWA certification, there are likely to be many homeowners who will have to pay additional money to rectify or remove the spray foam before a mortgage can be granted. As a first port of call, we recommend that any homeowner with spray foam in their roof, contact the installer to request condensation risk calculations and pre-install survey information along with guarantees and warranties if they do not already have this information.
Despite the bad press and negativity surrounding spray foam insulation, it is important not to panic, especially if you aren’t planning to sell your home anytime soon. Even if a spray foam installation is not compliant or up to modern standards, the impacts will materialise over a long period of time and its highly unlikely to have caused significant damage. As a homeowner with spray foam, it is essential to take the necessary steps provided in this narrative.
Inspection Protocol for Surveyors
The Inspection Protocol document was released in March 2023 to help guide surveyors when assessing a home where spray foam insulation has been installed. This document helps surveyors to identify whether a spray foam installation poses a low, medium, or high risk to the property, enabling conclusions to be drawn that can then be presented to the mortgage lender for sign-off. The Inspection Protocol is a significant step forward in understanding what represents a compliant installation, and we’ve already seen evidence that many lenders and surveyors have adopted this guidance.
An installation can potentially be classified as compliant and low risk where the following documents are available to the surveyor at the point of inspection:
A pre-installation survey report that identifies the roof condition, type of membrane and condition, moisture readings of existing structural timbers, existing ventilation strategies and photographs or videos.
A BBA or KIWA certificate that shows the type and brand of spray foam installed along with a project summary to explain the
A U-value and Condensation Risk Analysis, clearly identifying a pass or fail for the proposed insulation system and any ventilation strategy to manage risks (where present).
Post-installation photographs and videos to show the completed installation.
An Installers Warranty (usually 25 Years)
A 25-Year Products Warranty.
Any other applicable information or operation and maintenance documents.
A bona-fide, experienced, professional spray foam installation company should be fine providing such documentation. As a mandatory suite of documents that the spray foam industry is aware they must supply, these should help the surveyor and lender arrive at a reasonable conclusion that spray foam installation is low, medium or high risk to the property.
Current Status of Mortgage Lenders
We are beginning to see positive movements amongst mortgage lenders when they encounter homes with Spray Foam Insulation installed. Several lenders are proactively lending or at least taking a view on lending provided the installation is compliant and backed up with all the necessary documentation. We are aware that Nationwide Building Society, Santander, Halifax, NatWest, and Barclays all consider mortgage lending on homes with spray foam and there are several smaller, bespoke lenders who also take a more proactive view. An increasingly popular request is that an Insurance Backed Guarantee is issued to cover the installation and we’ve worked hard to team up with an insurance provider who will support spray foam installations carried out using our products and our approved network of installers.
Whilst there may be some negative articles on the internet about spray foam insulation and homeowners unable to sell their homes, this situation is rapidly changing as the realisation sets in that homeowners need to be given a choice of what products they can insulate their homes with. For anyone reading this article who may have read some negative press, we would recommend that you ask a few mortgage lenders on their stance when it comes to spray foam insulation before planning on whether to proceed with an installation. If lenders give a positive response and more are prepared to lend than not lend, you should feel a degree of confidence that the mortgage issue is moving on to a more positive approach. You can also be rest-assured that ThermoFoam support our approved installers and their customers every step of the way!
It is important to note that Equity Release Lenders take a much more risk adverse approach to spray foam insulation and we are not aware of any that offer mortgages on homes with spray foam. This is because the lending they offer is based on a stake in the property and assumption that the property will increase in value over the duration of the term, therefore, the lending criteria is very strict and there could be many types of home improvement product they might object to. In addition, we cannot confidently state that ALL mortgage lenders are accepting of spray foam insulation, but we are aware of some of the major high-street lenders who do accept it and we expect lending parameters to relax as the spray foam industry moves forward.
ThermoFoam’s Approach
We’re one of five spray foam insulation manufacturers/distributors based in the UK who have products that are certified by the BBA or KIWA. Product certification is a hallmark of trust, showing that the products have been tested, assessed, and approved for use in certain circumstances. Our Sucraseal Open Cell and Nexseal Closed Cell foams are rendered fit for purpose in various settings, including as a retrofit option in the pitched roofs of UK homes.
Our installer network is trained and approved by us for the various measures, and each installation company has been provided with an approved installer’s card. In addition, we also list our approved installers on our website so that you know you’re dealing with a bonafide contractor. Our training is rigorous, and those who use our materials in UK homes know they must consistently demonstrate high compliance.
In addition, we have also made it mandatory that our approved installers undergo approved installer status with the BBA. We must undertake several surveillance visits to completed installations each year, which helps us to ensure that our approved installers meet our expectations. With the BBA also undertaking independent surveillance, an approved installer is closely monitored to maintain high standards and compliance.
Our internal processes are designed to protect the homeowner and go beyond the standard expectations of the Inspection Protocol document. When a homeowner chooses Sucraseal or Nexseal for their home, they can be assured of the following:
The products are fit for purpose and can be used in the home.
Provided a ThermoFoam-approved installer is used, they hold the relevant valid insurances, they are BBA-approved and have subscribed to the ThermoFoam Code of Conduct and Best Practice guide.
The approved installer will conduct a full pre-installation assessment of the home to ensure the product’s intended use will meet its BBA certification requirements.
The approved installer will always follow ThermoFoam’s best practice guide to ensure installations are compliant and that the relevant evidence is captured correctly.
ThermoFoam assesses every installation remotely using the pre-installation survey report, photographs, and videos.
Product batch numbers are captured by the approved installer and matched to the Product Warranty.
Hygrothermal monitoring devices have been installed to measure relative humidity, temperature, and vapour pressure distribution through the building assembly.
High-resistance, non-breathable roofing membranes have been adequately ventilated using a spacing card to maintain a 50mm air gap above the insulation. (see the High Resistance Roof Coverings Policy).
A QR code label is placed in the loft space, providing the homeowner and any independent surveyor access to the suite of documents to evidence a compliant installation.
Spray Foam Pricing
Part of the PCA and RPSA’s dislike of the spray foam industry were a result of the questionable sales practices adopted by some companies. Home improvement products can sometimes be mis sold or at vastly inflated prices, and the spray foam industry is not free of forced sales and high-price tactics. Spray foam insulation is far from being the only home improvement product that is mis sold and this of course, doesn’t make it a bad, unnecessary, or unviable product. It is hard to monitor the pricing that our approved installers charge their customers, and to a degree, the price a product is sold for also depends on the running costs of the business installing it. Single-man operations will generally always be cheaper than larger organisations with higher overheads.
To assist a homeowner considering spray foam insulation, our Best Practice Guide recommends that an approved installer charges between £30-£55 per square metre. Often, spray foam sales companies may pitch the price closer to £100 per metre, and in those circumstances, we would always recommend that you get at least two other quotes before making your decision. We do not support brutal sales tactics or high pricing, and if an approved installer or sales company is pitching our products in a manner we don’t support, we will act.
Of course, different jobs can be more complex and require a higher per meter price, so a homeowner should always obtain a few comparable quotes before deciding. Low meterage jobs also generally attract a higher per meter rate due to the cost for the approved installer to mobilize the equipment to carry out the installation.
Should I Get Spray Foam?
Perhaps you have heard about spray foam through a friend, family member, direct approach, or an advert, you may be wondering whether its right for you. The answer is that spray foam insulation, will, in most circumstances, improve the thermal performance of the home and make a tangible difference to your comfort and your energy costs. Provided you approach a reputable spray foam company who has good online reviews, conducts a pre-installation survey of your property, and documents their suggested scope of works in a legible format, there is no reason why you shouldn’t choose spray foam insulation.
If you are worried about committing to an installation in the backdrop of some negative press, it’s important to remember that the RPSA and PCA initial report was later retracted and that since then, a huge amount of work has been undertaken by the working group to draw up a set of parameters that bring confidence to the product and its suitability. Simply because there’s a report that paints a negative image of spray foam, it doesn’t mean that the product isn’t safe or suitable for your home.
If you are in any doubt about mortgage lenders appetite to offer finance on homes with spray foam insulation present, we recommend that you reach out to some lenders to ask the question “I’m considering spray foam insulation for my pitched roof, do you offer mortgages on homes with spray foam?” We have customers who have done the same and the result was that several mortgage lenders will and do lend on homes where spray foam insulation has been installed.
Make sure the installer aims to deliver a solution that acts as a thermal upgrade to your home and doesn’t reduce the performance of any insulation materials already present. For example, installing 100mm of open cell spray foam insulation and removing 200mm of mineral wool on the loft floor will produce a result that is less thermally efficient than what’s already there!
Should I Get Spray Foam Removed?
If you are a homeowner with spray foam insulation installed in the pitched roof of your home, you may be in a state of panic that you won’t be able to re-mortgage or sell your home in the future. We would urge you to remain calm about any negative press you may have seen because in many circumstances, a mortgage lender should at least consider the installation before deciding. If you aren’t planning to sell or re-mortgage your home and unless you have noticed any issues in the home following the spray foam install, we wouldn’t recommend removing it for the sake of it. It will add unnecessary expense and it will reduce the benefits it’s having on your home through better thermal performance.
There are several items to consider if you already have spray foam installed in your home:
Were you provided with paperwork following the installation? This may include installers guarantee or product warranty.
Has the installer got photos or videos of the roof condition prior to the installation?
Does the spray foam look uniform and neat?
To your knowledge, did you have open cell or closed cell installed?
Was the installation to a roof membrane or direct to tile?
If to a membrane, was this low or high resistance?
Can the installer provide a retrospective hygrothermal or condensation risk assessment?
Is the brand of spray foam insulation used BBA or KIWA certified?
If your installer is still in business and there are gaps in the paperwork, they provided you with, we recommend contacting them to request this. If your installer is no longer in business but you know what brand of spray foam insulation was installed in your home, approach the manufacturer of that product for assistance – they may be able to provide you with some or all the required paperwork. If you didn’t have the spray foam installed and you don’t have any paperwork at all but there are no obvious signs of defect in the roof, you’re unlikely to experience any issues with the spray foam insulation and unless you are planning to move or re-mortgage, we wouldn’t recommend getting it removed.
Perhaps you are still uneasy about the situation and want further advice? We would recommend contacting a spray foam insulation distributor or manufacturer for advice. If you can provide some photos or videos of the installation, you will find many spray foam companies willing to offer their opinion on whether the installation looks compliant and whether you have open or closed cell insulation installed. Photos will usually show whether the foam has been installed to a roof membrane or direct-to-tile.
In many circumstances, homeowners have had spray foam insulation removed completely unnecessarily. This video explains how a closed cell installation to a breathable roof membrane showed no signs of roof rafter rot or degradation, six years following installation.
Spray Foam Insulation Consultancy Service
We now offer a consultancy service designed to assist homeowners with questions surrounding spray foam insulation. We’re passionate about spray foam insulation and its benefits but we also understand the circumstances that led the PCA and RPSA to highlight their initial concerns. It’s therefore essential to us that we work with homeowners, surveyors, lenders and other third parties to help the spray foam industry to navigate through these turbulent times. Whether you are a customer of ThermoFoam or you had your installation carried out by another company, we are able to help.
Initial Inspection & Reporting
If you have spray foam insulation installed or you are supporting a friend or family member, we can offer a spray foam health check by visiting your home to establish the following:
Paperwork assessment (don’t panic if you don’t have any paperwork). A quote or invoice related to the installation could be enough for us to establish who carried out the installation and what brand of spray foam was used.
Installation quality. We’ll quickly be able to determine the type of spray foam (open or closed cell), the thickness installed and whether it constitutes a compliant installation. It is important to note that the initial checks include checks to assess that the spray foam is hermetically sealed rafter to rafter. You can learn more about hermetic sealing here: https://thermofoam.co.uk/building-science-moisture-management/.
Membrane Assessment. We will need to remove a small area of the spray foam installation to determine what type or roof membrane it has been installed against. This will determine whether any remedial actions are required. Don’t worry, we’ll always fill in any areas where we remove the spray foam insulation.
Moisture Checks. We’ll use a moisture meter and hygrometer to assess the moisture content in the roof rafter faces, inner rafter faces and the outer 1cm layer of the insulation closest to the membrane. Again, this will require the removal of a small section of spray foam on each roof elevation but we will re-seal this.
Roof Assessment. We’ll conduct an internal and external roof assessment to determine the general condition of the roof. This involves assessing for any slipped or broken tiles, lead flashing around chimneys and the condition of roof tiles. Part of the assessment will be conducted using the principles of our pre-install survey protocol which can be viewed here: https://thermofoam.co.uk/pre-install-surveys/
Hygrothermal Assessment: We’ll use our findings to provide a bespoke hygrothermal assessment that considers the condensation risk associated with the spray foam install along with the thermal performance of the entire insulation assembly within the attic space. To find out more about hygrothermal assessments, you can read our article here: https://thermofoam.co.uk/independent-hygrothermal-studies/
Formal Report: We’ll issue a formal written report that summarizes the evidence collected during the assessment. This will include the inspection summary, evidence of findings and our conclusion as to whether the installation should be deemed a low, medium or high risk. Additionally, we’ll recommend the next steps to take and build an evaluation pack that you can use to present to building surveyors, mortgage lenders and prospective buyers in the future.
The cost of this service is £295 plus VAT with a 50% deposit paid upon booking and the remaining 50% payable before we issue the Formal Report.
Remedial Actions
The formal report will give the installation a risk rating of low, medium or high. The remedial actions required may vary on a case by case basis and can be determined as follows:
Low Risk (Green):
The insulation (open or closed cell) has been installed to a breathable roof membrane or rafter slide ventilation card. See our article on rafter slide ventilation here: https://thermofoam.co.uk/rafter-ventilation-system/.
The insulation is at at least 50mm in thickness for closed cell and at least 100mm in thickness for open cell and has been applied evenly throughout each roof rafter bay.
The insulation is hermetically sealed, rafter to rafter, with no visible signs of shrinkage or delamination from roof rafter edges or sides. See our article on building science and hermetical sealing here: https://thermofoam.co.uk/building-science-moisture-management/.
There are no evident signs of internal or external roof problems or potential for roof leaks.
The moisture content in the roof rafters
Closing Summary
The negativity surrounding spray foam insulation doesn’t make it a bad product that a homeowner should avoid. Modern Building Regulations support the theory of spray foam insulation because buildings need to be airtight and more thermally effective. When airtight insulation is installed, additional ventilation or vapour control layers should be considered if the risk of condensation is heightened.
The BBA and KIWA approve many thousands of construction and insulation materials for their suitability. Despite the opinions of some surveyors and lenders, the validity of a BBA/KIWA certificate cannot be questioned if the product has been installed in accordance with the guidance. Whether or not a product or material has been installed following that certification is another matter. Our internal processes help to ensure that the expected standard is always met, and any installers who do not subscribe to our Code of Conduct and Best Practice Guide are automatically suspended from our network until they can demonstrate compliance.
A wide range of insulation materials are available in the UK, and it is always important to weigh up whether the proposed system is suitable for your property and meets your affordability. Spray Foam Insulation is undoubtedly a premium option compared to mineral wool rolls laid on the loft floor because it is airtight, not subject to the shrinkage or degradation mineral wool can suffer and at roof level, it protects the envelope of property from solar gain and heat loss. Still, every insulation product has a thermal conductivity and 100mm of open cell spray foam is not as thermally efficient as 300mm of mineral wool on the loft floor. In some scenarios, spray foam can complement a mineral wool installation on the loft floor, provided a condensation risk analysis has been carried out first.
Do your research.
Choose BBA or KIWA Certified products.
Get three comparative quotes.
Make sure the installer gives you a handover pack.
If in doubt, get in touch with us.
Importantly, don’t panic, there are many people in the spray foam industry who want to support homeowners who have spray foam installed. On the most part, we are a knowledgeable, experienced, and compliant industry who only want to do what’s right for people and their homes! We cannot honestly say that a homeowner with spray foam insulation or considering having it installed won’t experience mortgage problems in the future but with several lenders now open for business and prepared to consider a spray foam installed that has been carried out correctly and with the necessary paperwork to back it up, there is a high chance that you will experience no issues.
Original article is provided by our partners and spray foam providers - ThermoFoam, it can be found following this link.
Introduction:
If you are reading this article, you may be looking for answers to the following questions:
Should I get spray foam in my home?
Does spray foam insulation cause rot?
Can I sell my home with spray foam?
Can I get a mortgage with spray foam?
What can I do if I have spray foam?
Can spray foam be removed?
We’ve created this article to help provide an honest appraisal of the situation related to spray foam insulation in existing homes and the problem of homeowners whose prospective buyers can’t always get mortgages as a result. We hope that you find this article provides some clarity about spray foam insulation and why some mortgage lenders paused lending for a short period until certain industry standards were identified and implemented. Despite a rise in opportunistic companies offering spray foam removal services, removal should always be the very last option for a homeowner.
Overview
It’s no secret that the Spray Foam Industry has been in the spotlight recently regarding some homes being rejected for a mortgage. The discussions about the suitability of Spray Foam Insulation when used in a home’s pitched roof area started in November 2021 when the PCA and RPSA issued a joint report highlighting their concerns over the product and its use.
The document highlighted concerns about the correct installation of open and closed cell foams, the science behind the product, the quality of the installers, the sales process and the documentary evidence handed over to the customer once an installation had taken place. Whilst the documentation released was somewhat damning about the spray foam industry, it also served as a chance for it to come together with the PCA, RPSA, various mortgage lenders, building surveyors and other notable industry experts to discuss concerns and implement practices that could provide reassurance.
In late 2022, a Working Group was established to create the parameters for a new inspection protocol that should guide surveyors and lenders when they encounter homes with spray foam insulation. The documents’ purpose was to offer guidance to building surveyors so that they could conclude whether the insulation posed a low, medium or high risk to the property.
Much of the dislike or concerns with spray foam are because it is spray-applied to the underside of the roof membrane, therefore covering the roof from the underside and limiting a surveyor’s ability to assess the condition of the roof. Whilst this is a justified concern, it is worth noting that there are many instances where a surveyor would be unable to see the underside of the roof to assess its condition, for example, in Dormer Bungalows. Of course, in many cases, surveyors were unable to review documentation that supported the purpose and considered the risks of having spray foam insulation installed. Additionally, most existing homes have a high-resistance, non-breathable bitumen felt-style membrane which can present internal moisture from escaping from the home. When these concerns are considered, it is easy to understand why there is much confusion over what constitutes a good or bad spray foam installation.
What Is Spray Foam Insulation?
There are two types of spray foam insulation: a high-density, partially breathable closed-cell foam and a low-density, very-breathable open-cell foam. Closed-cell foam was introduced into the UK in the 1980s and was mainly used in industrial environments. It also found its way into UK homes thanks to its ability to bond and strengthen failing roofs where roofing membranes were damaged or weren’t present. Whilst effective at prolonging the life of a roof, closed-cell foam can also cause enhanced decay of the structure if moisture becomes trapped within the roof structure. This was a point led the PCA and RPSA to highlight the risks of spray foam insulation.
Open Cell Foam is a low-density, breathable product that started to gain popularity from 2012 onwards. Sprayed directly to the underside of roofing felts, it provides an airtight yet breathable thermal seal of the roof space, which helps to conserve energy and make a home more energy efficient. In addition, Open Cell spray foam can offer excellent sound attenuation whilst freeing up space on the loft floor for storage. It can also perform with the life of the property without degrading or deteriorating, often guaranteed by the installer for a period of 25-years.
When installed as a direct-to-tile, roof stabilisation system, the roof itself maybe experiencing fatigue and may have reached the end of its natural life, therefore requiring replacement. Whilst closed-cell foam is very effective at extending the life of the roof for an indefinite period, naturally, many homeowners saw it as a cheaper alternative to replacing the replacing the roof. Interest from homeowners was not least because some spray foam companies were activity promoting roof stabilisation solutions in the national press. Whilst previously certified as an accepted practice, direct to tile, roof stabilisation is no longer endorsed, certified or accepted as a viable option and when the roof has come to the end of its natural life, the only option is for replacement.
As insulation and thermal upgrades have become such an important part of helping homeowners to control energy costs and reduce their carbon footprint, open cell foam grew in popularity throughout the 2010’s. During the 2020-2021 Government Green Homes Grant, spray foam insulation was an approved installation measure which saw a rapid growth of its use in UK homes. The Green Homes Grant saw many installers become PAS 2030 certified which led to more stringent lodgements of installations onto the Trustmark database along with the opportunity for more surveillance of installers by the certification bodies issuing the PAS 2030 accreditations.
You can also learn more about the science behind spray foam insulation by visiting our article here: https://vpfoamspray.co.uk/about#sfi
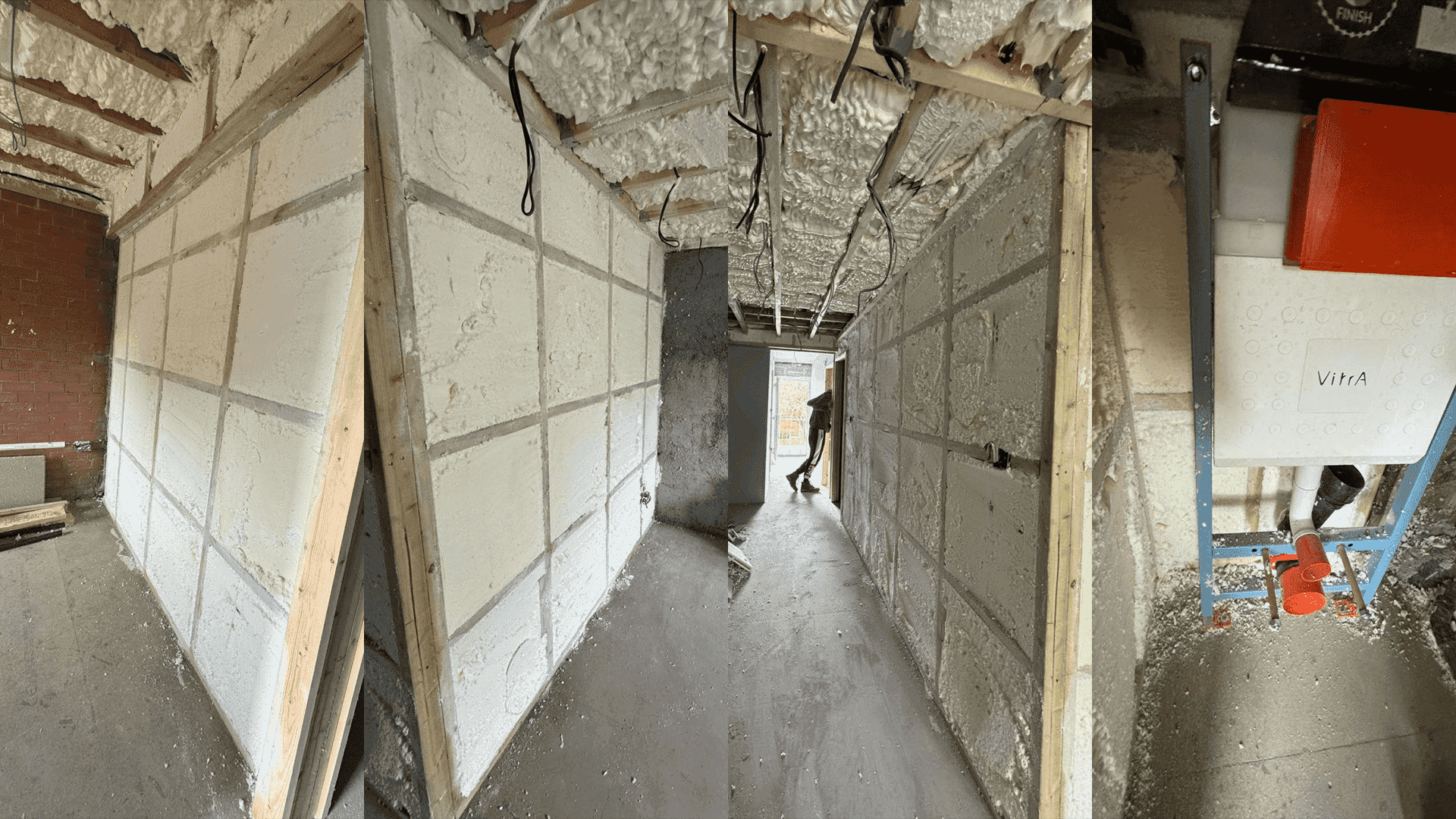
Spray Foam Mortgage Issues
Until earlier in 2023, mortgage lenders had paused offering mortgage lending on homes where spray foam insulation was installed. As a result of the Inspection Protocol documents and the efforts of the Working Group, several lenders are now prepared to accept spray foam as a viable insulation material, provided there is evidence and paperwork to show that it has been installed correctly as per approved product certification in the form of a BBA or KIWA certificate. Whilst there is a long way to go to dispel the myths of spray foam insulation completely, good progress has been made and will continue to be made but thats not to say there aren’t a vast number of non-compliant and shoddy installations that require remedy or removal.
Closed Cell Foam, when applied directly to roof tiles, is no longer an accepted insulation method due to the elevated risks attached to its application. Conversely, open cell foam, installed directly to a low-resistance roof membrane, is a very low-risk installation provided the roof is in good condition before installation and all necessary evidence has been compiled to show a compliant installation. When high resistance, bitumen felt style membranes are in situ, spray foam can still be installed, with consideration that a ventilation card should be inserted between the rafters to create airflow above the insulation or a vapour control layer is installed to the warm side of the spray foam insulation. BBA and KIWA certification recommend that a condensation risk analysis is conducted prior to the installation of spray foam insulation and most, if not all manufacturers and distributors now support their customers with this documentation. Additionally, closed cell spray foam, installed directly to high-resistance, bitumen felt-style membranes can also be classed as low-risk in southern areas of the UK.
It is essential to highlight that the RPSA and PCA Joint Position on Spray Foam Insulation, released in November 2021, was retracted in October 2022. This doesn’t mean the findings highlighted in the initial statement weren’t relevant or required further action. Still, it did help to cool the frustration between various bodies, enabling proactive discussions to take place. Under Government Guidance, the surveying, lending, and spray foam industry came together in what was an industry first and a milestone in establishing a more compliant future for this insulation material.
Fundamentally, if installed correctly in conjunction with BBA or KIWA certification, homeowners, lenders, and surveyors should feel comfortable that spray foam is a viable insulation solution for a home. In return, manufacturers/distributors, such as us, must ensure that the installers who buy our materials are adequately trained, subscribe to, and follow a set of principles that meet modern regulations. If the industry can move towards providing evidence, rationale, and science to support an installation, the spray foam mortgage issues will likely become a thing of the past.
Of course, this doesn’t help homeowners who have already had spray foam installed. With a reported 250,000 homes that have spray foam already installed, it’s likely that without the evidence that the spray foam was installed correctly following its BBA or KIWA certification, there are likely to be many homeowners who will have to pay additional money to rectify or remove the spray foam before a mortgage can be granted. As a first port of call, we recommend that any homeowner with spray foam in their roof, contact the installer to request condensation risk calculations and pre-install survey information along with guarantees and warranties if they do not already have this information.
Despite the bad press and negativity surrounding spray foam insulation, it is important not to panic, especially if you aren’t planning to sell your home anytime soon. Even if a spray foam installation is not compliant or up to modern standards, the impacts will materialise over a long period of time and its highly unlikely to have caused significant damage. As a homeowner with spray foam, it is essential to take the necessary steps provided in this narrative.
Inspection Protocol for Surveyors
The Inspection Protocol document was released in March 2023 to help guide surveyors when assessing a home where spray foam insulation has been installed. This document helps surveyors to identify whether a spray foam installation poses a low, medium, or high risk to the property, enabling conclusions to be drawn that can then be presented to the mortgage lender for sign-off. The Inspection Protocol is a significant step forward in understanding what represents a compliant installation, and we’ve already seen evidence that many lenders and surveyors have adopted this guidance.
An installation can potentially be classified as compliant and low risk where the following documents are available to the surveyor at the point of inspection:
A pre-installation survey report that identifies the roof condition, type of membrane and condition, moisture readings of existing structural timbers, existing ventilation strategies and photographs or videos.
A BBA or KIWA certificate that shows the type and brand of spray foam installed along with a project summary to explain the
A U-value and Condensation Risk Analysis, clearly identifying a pass or fail for the proposed insulation system and any ventilation strategy to manage risks (where present).
Post-installation photographs and videos to show the completed installation.
An Installers Warranty (usually 25 Years)
A 25-Year Products Warranty.
Any other applicable information or operation and maintenance documents.
A bona-fide, experienced, professional spray foam installation company should be fine providing such documentation. As a mandatory suite of documents that the spray foam industry is aware they must supply, these should help the surveyor and lender arrive at a reasonable conclusion that spray foam installation is low, medium or high risk to the property.
Current Status of Mortgage Lenders
We are beginning to see positive movements amongst mortgage lenders when they encounter homes with Spray Foam Insulation installed. Several lenders are proactively lending or at least taking a view on lending provided the installation is compliant and backed up with all the necessary documentation. We are aware that Nationwide Building Society, Santander, Halifax, NatWest, and Barclays all consider mortgage lending on homes with spray foam and there are several smaller, bespoke lenders who also take a more proactive view. An increasingly popular request is that an Insurance Backed Guarantee is issued to cover the installation and we’ve worked hard to team up with an insurance provider who will support spray foam installations carried out using our products and our approved network of installers.
Whilst there may be some negative articles on the internet about spray foam insulation and homeowners unable to sell their homes, this situation is rapidly changing as the realisation sets in that homeowners need to be given a choice of what products they can insulate their homes with. For anyone reading this article who may have read some negative press, we would recommend that you ask a few mortgage lenders on their stance when it comes to spray foam insulation before planning on whether to proceed with an installation. If lenders give a positive response and more are prepared to lend than not lend, you should feel a degree of confidence that the mortgage issue is moving on to a more positive approach. You can also be rest-assured that ThermoFoam support our approved installers and their customers every step of the way!
It is important to note that Equity Release Lenders take a much more risk adverse approach to spray foam insulation and we are not aware of any that offer mortgages on homes with spray foam. This is because the lending they offer is based on a stake in the property and assumption that the property will increase in value over the duration of the term, therefore, the lending criteria is very strict and there could be many types of home improvement product they might object to. In addition, we cannot confidently state that ALL mortgage lenders are accepting of spray foam insulation, but we are aware of some of the major high-street lenders who do accept it and we expect lending parameters to relax as the spray foam industry moves forward.
ThermoFoam’s Approach
We’re one of five spray foam insulation manufacturers/distributors based in the UK who have products that are certified by the BBA or KIWA. Product certification is a hallmark of trust, showing that the products have been tested, assessed, and approved for use in certain circumstances. Our Sucraseal Open Cell and Nexseal Closed Cell foams are rendered fit for purpose in various settings, including as a retrofit option in the pitched roofs of UK homes.
Our installer network is trained and approved by us for the various measures, and each installation company has been provided with an approved installer’s card. In addition, we also list our approved installers on our website so that you know you’re dealing with a bonafide contractor. Our training is rigorous, and those who use our materials in UK homes know they must consistently demonstrate high compliance.
In addition, we have also made it mandatory that our approved installers undergo approved installer status with the BBA. We must undertake several surveillance visits to completed installations each year, which helps us to ensure that our approved installers meet our expectations. With the BBA also undertaking independent surveillance, an approved installer is closely monitored to maintain high standards and compliance.
Our internal processes are designed to protect the homeowner and go beyond the standard expectations of the Inspection Protocol document. When a homeowner chooses Sucraseal or Nexseal for their home, they can be assured of the following:
The products are fit for purpose and can be used in the home.
Provided a ThermoFoam-approved installer is used, they hold the relevant valid insurances, they are BBA-approved and have subscribed to the ThermoFoam Code of Conduct and Best Practice guide.
The approved installer will conduct a full pre-installation assessment of the home to ensure the product’s intended use will meet its BBA certification requirements.
The approved installer will always follow ThermoFoam’s best practice guide to ensure installations are compliant and that the relevant evidence is captured correctly.
ThermoFoam assesses every installation remotely using the pre-installation survey report, photographs, and videos.
Product batch numbers are captured by the approved installer and matched to the Product Warranty.
Hygrothermal monitoring devices have been installed to measure relative humidity, temperature, and vapour pressure distribution through the building assembly.
High-resistance, non-breathable roofing membranes have been adequately ventilated using a spacing card to maintain a 50mm air gap above the insulation. (see the High Resistance Roof Coverings Policy).
A QR code label is placed in the loft space, providing the homeowner and any independent surveyor access to the suite of documents to evidence a compliant installation.
Spray Foam Pricing
Part of the PCA and RPSA’s dislike of the spray foam industry were a result of the questionable sales practices adopted by some companies. Home improvement products can sometimes be mis sold or at vastly inflated prices, and the spray foam industry is not free of forced sales and high-price tactics. Spray foam insulation is far from being the only home improvement product that is mis sold and this of course, doesn’t make it a bad, unnecessary, or unviable product. It is hard to monitor the pricing that our approved installers charge their customers, and to a degree, the price a product is sold for also depends on the running costs of the business installing it. Single-man operations will generally always be cheaper than larger organisations with higher overheads.
To assist a homeowner considering spray foam insulation, our Best Practice Guide recommends that an approved installer charges between £30-£55 per square metre. Often, spray foam sales companies may pitch the price closer to £100 per metre, and in those circumstances, we would always recommend that you get at least two other quotes before making your decision. We do not support brutal sales tactics or high pricing, and if an approved installer or sales company is pitching our products in a manner we don’t support, we will act.
Of course, different jobs can be more complex and require a higher per meter price, so a homeowner should always obtain a few comparable quotes before deciding. Low meterage jobs also generally attract a higher per meter rate due to the cost for the approved installer to mobilize the equipment to carry out the installation.
Should I Get Spray Foam?
Perhaps you have heard about spray foam through a friend, family member, direct approach, or an advert, you may be wondering whether its right for you. The answer is that spray foam insulation, will, in most circumstances, improve the thermal performance of the home and make a tangible difference to your comfort and your energy costs. Provided you approach a reputable spray foam company who has good online reviews, conducts a pre-installation survey of your property, and documents their suggested scope of works in a legible format, there is no reason why you shouldn’t choose spray foam insulation.
If you are worried about committing to an installation in the backdrop of some negative press, it’s important to remember that the RPSA and PCA initial report was later retracted and that since then, a huge amount of work has been undertaken by the working group to draw up a set of parameters that bring confidence to the product and its suitability. Simply because there’s a report that paints a negative image of spray foam, it doesn’t mean that the product isn’t safe or suitable for your home.
If you are in any doubt about mortgage lenders appetite to offer finance on homes with spray foam insulation present, we recommend that you reach out to some lenders to ask the question “I’m considering spray foam insulation for my pitched roof, do you offer mortgages on homes with spray foam?” We have customers who have done the same and the result was that several mortgage lenders will and do lend on homes where spray foam insulation has been installed.
Make sure the installer aims to deliver a solution that acts as a thermal upgrade to your home and doesn’t reduce the performance of any insulation materials already present. For example, installing 100mm of open cell spray foam insulation and removing 200mm of mineral wool on the loft floor will produce a result that is less thermally efficient than what’s already there!
Should I Get Spray Foam Removed?
If you are a homeowner with spray foam insulation installed in the pitched roof of your home, you may be in a state of panic that you won’t be able to re-mortgage or sell your home in the future. We would urge you to remain calm about any negative press you may have seen because in many circumstances, a mortgage lender should at least consider the installation before deciding. If you aren’t planning to sell or re-mortgage your home and unless you have noticed any issues in the home following the spray foam install, we wouldn’t recommend removing it for the sake of it. It will add unnecessary expense and it will reduce the benefits it’s having on your home through better thermal performance.
There are several items to consider if you already have spray foam installed in your home:
Were you provided with paperwork following the installation? This may include installers guarantee or product warranty.
Has the installer got photos or videos of the roof condition prior to the installation?
Does the spray foam look uniform and neat?
To your knowledge, did you have open cell or closed cell installed?
Was the installation to a roof membrane or direct to tile?
If to a membrane, was this low or high resistance?
Can the installer provide a retrospective hygrothermal or condensation risk assessment?
Is the brand of spray foam insulation used BBA or KIWA certified?
If your installer is still in business and there are gaps in the paperwork, they provided you with, we recommend contacting them to request this. If your installer is no longer in business but you know what brand of spray foam insulation was installed in your home, approach the manufacturer of that product for assistance – they may be able to provide you with some or all the required paperwork. If you didn’t have the spray foam installed and you don’t have any paperwork at all but there are no obvious signs of defect in the roof, you’re unlikely to experience any issues with the spray foam insulation and unless you are planning to move or re-mortgage, we wouldn’t recommend getting it removed.
Perhaps you are still uneasy about the situation and want further advice? We would recommend contacting a spray foam insulation distributor or manufacturer for advice. If you can provide some photos or videos of the installation, you will find many spray foam companies willing to offer their opinion on whether the installation looks compliant and whether you have open or closed cell insulation installed. Photos will usually show whether the foam has been installed to a roof membrane or direct-to-tile.
In many circumstances, homeowners have had spray foam insulation removed completely unnecessarily. This video explains how a closed cell installation to a breathable roof membrane showed no signs of roof rafter rot or degradation, six years following installation.
Spray Foam Insulation Consultancy Service
We now offer a consultancy service designed to assist homeowners with questions surrounding spray foam insulation. We’re passionate about spray foam insulation and its benefits but we also understand the circumstances that led the PCA and RPSA to highlight their initial concerns. It’s therefore essential to us that we work with homeowners, surveyors, lenders and other third parties to help the spray foam industry to navigate through these turbulent times. Whether you are a customer of ThermoFoam or you had your installation carried out by another company, we are able to help.
Initial Inspection & Reporting
If you have spray foam insulation installed or you are supporting a friend or family member, we can offer a spray foam health check by visiting your home to establish the following:
Paperwork assessment (don’t panic if you don’t have any paperwork). A quote or invoice related to the installation could be enough for us to establish who carried out the installation and what brand of spray foam was used.
Installation quality. We’ll quickly be able to determine the type of spray foam (open or closed cell), the thickness installed and whether it constitutes a compliant installation. It is important to note that the initial checks include checks to assess that the spray foam is hermetically sealed rafter to rafter. You can learn more about hermetic sealing here: https://thermofoam.co.uk/building-science-moisture-management/.
Membrane Assessment. We will need to remove a small area of the spray foam installation to determine what type or roof membrane it has been installed against. This will determine whether any remedial actions are required. Don’t worry, we’ll always fill in any areas where we remove the spray foam insulation.
Moisture Checks. We’ll use a moisture meter and hygrometer to assess the moisture content in the roof rafter faces, inner rafter faces and the outer 1cm layer of the insulation closest to the membrane. Again, this will require the removal of a small section of spray foam on each roof elevation but we will re-seal this.
Roof Assessment. We’ll conduct an internal and external roof assessment to determine the general condition of the roof. This involves assessing for any slipped or broken tiles, lead flashing around chimneys and the condition of roof tiles. Part of the assessment will be conducted using the principles of our pre-install survey protocol which can be viewed here: https://thermofoam.co.uk/pre-install-surveys/
Hygrothermal Assessment: We’ll use our findings to provide a bespoke hygrothermal assessment that considers the condensation risk associated with the spray foam install along with the thermal performance of the entire insulation assembly within the attic space. To find out more about hygrothermal assessments, you can read our article here: https://thermofoam.co.uk/independent-hygrothermal-studies/
Formal Report: We’ll issue a formal written report that summarizes the evidence collected during the assessment. This will include the inspection summary, evidence of findings and our conclusion as to whether the installation should be deemed a low, medium or high risk. Additionally, we’ll recommend the next steps to take and build an evaluation pack that you can use to present to building surveyors, mortgage lenders and prospective buyers in the future.
The cost of this service is £295 plus VAT with a 50% deposit paid upon booking and the remaining 50% payable before we issue the Formal Report.
Remedial Actions
The formal report will give the installation a risk rating of low, medium or high. The remedial actions required may vary on a case by case basis and can be determined as follows:
Low Risk (Green):
The insulation (open or closed cell) has been installed to a breathable roof membrane or rafter slide ventilation card. See our article on rafter slide ventilation here: https://thermofoam.co.uk/rafter-ventilation-system/.
The insulation is at at least 50mm in thickness for closed cell and at least 100mm in thickness for open cell and has been applied evenly throughout each roof rafter bay.
The insulation is hermetically sealed, rafter to rafter, with no visible signs of shrinkage or delamination from roof rafter edges or sides. See our article on building science and hermetical sealing here: https://thermofoam.co.uk/building-science-moisture-management/.
There are no evident signs of internal or external roof problems or potential for roof leaks.
The moisture content in the roof rafters
Closing Summary
The negativity surrounding spray foam insulation doesn’t make it a bad product that a homeowner should avoid. Modern Building Regulations support the theory of spray foam insulation because buildings need to be airtight and more thermally effective. When airtight insulation is installed, additional ventilation or vapour control layers should be considered if the risk of condensation is heightened.
The BBA and KIWA approve many thousands of construction and insulation materials for their suitability. Despite the opinions of some surveyors and lenders, the validity of a BBA/KIWA certificate cannot be questioned if the product has been installed in accordance with the guidance. Whether or not a product or material has been installed following that certification is another matter. Our internal processes help to ensure that the expected standard is always met, and any installers who do not subscribe to our Code of Conduct and Best Practice Guide are automatically suspended from our network until they can demonstrate compliance.
A wide range of insulation materials are available in the UK, and it is always important to weigh up whether the proposed system is suitable for your property and meets your affordability. Spray Foam Insulation is undoubtedly a premium option compared to mineral wool rolls laid on the loft floor because it is airtight, not subject to the shrinkage or degradation mineral wool can suffer and at roof level, it protects the envelope of property from solar gain and heat loss. Still, every insulation product has a thermal conductivity and 100mm of open cell spray foam is not as thermally efficient as 300mm of mineral wool on the loft floor. In some scenarios, spray foam can complement a mineral wool installation on the loft floor, provided a condensation risk analysis has been carried out first.
Do your research.
Choose BBA or KIWA Certified products.
Get three comparative quotes.
Make sure the installer gives you a handover pack.
If in doubt, get in touch with us.
Importantly, don’t panic, there are many people in the spray foam industry who want to support homeowners who have spray foam installed. On the most part, we are a knowledgeable, experienced, and compliant industry who only want to do what’s right for people and their homes! We cannot honestly say that a homeowner with spray foam insulation or considering having it installed won’t experience mortgage problems in the future but with several lenders now open for business and prepared to consider a spray foam installed that has been carried out correctly and with the necessary paperwork to back it up, there is a high chance that you will experience no issues.